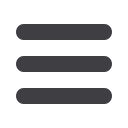

13
FIX MASTER BLIND RIVETS
Riveting is very reliable and widely used technique for fastening materials together permanently.
For best results following instructions should be observed:
Joint strength
Determine the shearing and tensile strengths that are required for the joint. They are fullfilled by using adequate number of rivets with right sizes and materials
Workpiece materials
When joining materials with different thickness or strengths the stronger material must be on the blind side of the joint. For example when fastening plastic and steel together the plastic piece should be
under the rivet head and the steel on the blind side.
Rivet diameter
In heavy load applications the rivet diameter should be at least equal to the thickest sheet thickness but not more than 3X the sheet under the rivet head.
Rivet length
Recommended length is the same as thickness of the workpiece materials (S) added by the rivet diameter (d). L = S + d
Grip range S (min-max)
The maximum thickness of the jointing workpieces when the hole diamater is according to the given values. The possible gap between the sheets must be included in the grip range calculation.
Hole diameter
Drilled or punched holes must be free of burrs in order to achieve reliable joint. In many cases the rivet fixes well into a hole which is maximum 0,1 mm bigger than the rivet’s nominal diameter.
Edge distance
Rivet hole distance from an edge should be at least 2X rivet diameter but not more than 24X.
Rivet distance
In high strength joints the distance between rivets should not be more than 3X rivet diameter.
Rivet material
The right rivet material is typically chosen to achieve the required strength in the joint. If the chosen rivet material differs from the workpiece material it is important to notice the risk of galvanic corrosion.
TECHNICAL INFORMATION